Molybdenum and Molybdenum Alloys: Demand and Applications
From the perspective of the global consumption structure, molybdenum is indeed an ally of iron. According to the demand table for molybdenum in western developed countries below, stainless steel accounts for 30%, low alloy steel accounts for 30%, drilling bits and cutting tools account for 10%, and cast steel accounts for 10%; the other 20% of molybdenum consumption is in molybdenum chemicals, molybdenum-based lubricants and petroleum refining. That is, nearly 80% of the demand for molybdenum stems from the demand for steel.
Molybdenum alloy
Molybdenum alloy has high-temperature strength, good electrical and thermal conductivity and low thermal expansion coefficient, and also has the advantage of easy processing. Molybdenum alloy materials such as plates, strips, foils, tubes, rods, wires and profiles are widely used in electronic tubes, electric light source parts, metal processing tools and turbine disks and other components.
Titanium Zirconium Molybdenum (TZM) alloy is the most widely used molybdenum alloy, which accounts for 15% of the total amount of molybdenum demand. It has excellent high temperature strength and comprehensive properties. The United States uses TZM alloy to make the turbine disk of the engine.
Titanium Zirconium Carbon (TZC) molybdenum alloy has high temperature mechanical properties than pure molybdenum, and are widely used in the manufacture of high temperature tools, molds and various structural parts.
Molybdenum-rhenium alloy has excellent high temperature performance and can be used at temperatures close to its melting point. It is used as brackets, rings, grids and other parts for thermowells and electron tube cathodes.
Molybdenum as an alloying element of steel
Molybdenum, together with nickel and chromium, acts as an alloying element to reduce the brittleness that often occurs in alloyed steels during heat treatment. Replacing tungsten with molybdenum in high-speed steel can solve the problem of insufficient tungsten resources. The role of molybdenum in stainless steel is to improve corrosion resistance, increase high temperature strength and improve weldability.
Other applications
Molybdenum has an extremely low vapor pressure at the temperatures and pressures at which vacuum furnaces operate. Therefore, molybdenum parts have the least pollution to the workpiece or working material in the furnace, and evaporation loss will not limit the service life of molybdenum high-temperature parts.
The high temperature strength of molybdenum makes it an ideal electrode and handling and processing equipment in glass manufacturing processes. In addition, molybdenum is chemically compatible with most glass components and therefore does not cause chromophoric effects. The life of molybdenum heating electrodes in glass melting furnaces can be as long as 3 to 5 years.
For more information, please visit https://www.samaterials.com/.
Related Posts
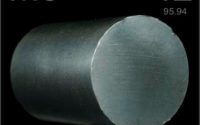
Metal for the Future: Molybdenum
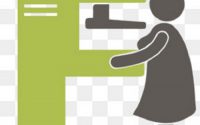
Guardian of Women’s Health: Molybdenum Target Inspection
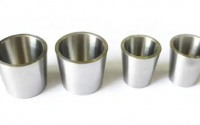