Advanced Superalloys for High-Temperature Applications
Introduction
Advanced superalloys are engineered metallic materials known for their outstanding mechanical strength and ability to resist surface degradation, including oxidation and corrosion. They work well, especially in environments with high temperatures. These materials are pivotal in industries where components are exposed to extreme conditions. Such fields include aerospace, power generation, and petrochemical processing.
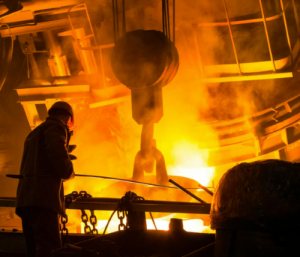
This article delves into the world of these high-temperature materials. Hope that you can learn about their characteristics, composition, development, and key high-temperature applications.
Characteristics of Advanced Superalloys
Advanced superalloys stand out due to their extraordinary characteristics. They have become crucial for high-demand engineering tasks. Their main features include:
- High-Temperature Strength: They maintain structural integrity under extreme thermal stress, so they can resist creep and other forms of deformation.
- Corrosion and Oxidation Resistance: Superalloys are less susceptible to environmental degradation, even in aggressive conditions.
- Thermal Stability: They retain their mechanical properties over a wide temperature range. Therefore, they are suitable for applications involving rapid temperature changes.
- Toughness: These high-temperature materials exhibit good resistance to fracture. That’s essential for safety-critical components.
Related reading: High-Temperature Alloys: Inconel, Hastelloy, And Beyond
Composition and Types of Advanced Superalloys
Superalloys are primarily composed of nickel, cobalt, or iron. They come with a complex mix of other elements such as chromium, molybdenum, tungsten, aluminum, and titanium. These elements are carefully balanced to achieve a specific set of properties tailored to demanding applications. The three main types of superalloys are:
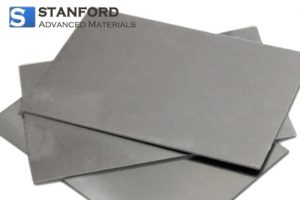
Nickel-based Superalloys: This most common type offers excellent high-temperature strength and corrosion resistance. Examples include Inconel, Hastelloy, and Waspaloy.
- Cobalt-based Superalloys: These high-temperature materials are notable for their wear resistance and stability under thermal cycling. Examples include Stellite and Haynes.
- Iron-based Superalloys: For instance, Fe-Ni alloys are less common but offer a cost-effective solution with moderate temperature resistance.
Development and Manufacturing
The development of advanced superalloys involves sophisticated metallurgical processes to optimize their microstructure for specific applications. Techniques such as vacuum melting, powder metallurgy, and single-crystal growth are employed to enhance purity and directional strength. Additive manufacturing (3D printing) has also emerged as a revolutionary method for producing complex superalloy components with minimal waste and enhanced performance characteristics.
Key Applications of Superalloys
Advanced superalloys play a pivotal role in sectors where endurance against intense stress and heat is paramount. Their key applications include:
- Aerospace: Within both commercial and military jet engines, superalloys are vital for high-temperature operation components such as discs, blades, and casings.
- Power Generation: Superalloys contribute to the efficiency of gas turbines by facilitating higher combustion temperatures, which in turn enhances performance and lowers emissions.
- Petrochemical Industry: In this sector, these high-temperature materials find their use in reactors, piping, and other equipment that must resist corrosion while operating at elevated temperatures.
- Automotive: High-performance automotive engines rely on superalloys for parts that need to endure extreme conditions of heat and pressure.
Challenges and Future Directions
- Despite their advantages, the development and use of advanced superalloys face challenges such as high material and processing costs, and the need for continued improvement in temperature capability and environmental resistance.
- Research is ongoing into new alloy compositions, manufacturing techniques, and surface treatments to address these challenges.
- Innovations in computational materials science are also playing a key role in accelerating the development of next-generation superalloys.
Conclusion
Advanced superalloys for high-temperature applications represent a critical field of materials science. These high-temperature materials continue to push the boundaries of what is possible in engineering and technology. Their development not only enhances the performance and efficiency of current systems but also paves the way for innovations in sectors crucial for the advancement of society.
Advanced Refractory Metals (ARM) stands as a reputable supplier of superalloys. ARM collaborates with global partners to deliver the highest quality at the most competitive prices. We tailor our manufacturing processes to meet your exact specifications. Send us an inquiry if you are interested.