Common Types of Rocket Nozzle Materials
Introduction
Rocket nozzles are critical components in propulsion systems, responsible for converting the thermal and chemical energy of the propellant into kinetic energy, thus generating thrust. Selecting the appropriate materials for rocket nozzles is vital due to the extreme operating conditions, including high temperatures, pressures, and corrosive environments. Here, we explore the common types of materials used in rocket nozzles and their respective advantages and applications.
1. Refractory Metals
- Tungsten (W):
Tungsten is renowned for its high melting point (3422°C) and excellent thermal conductivity. These properties make it an ideal material for rocket nozzles, particularly in applications where extreme heat resistance is required. Tungsten’s high density also contributes to its effectiveness in withstanding the erosive forces encountered during rocket engine operation. However, its brittleness and difficulty in machining present significant challenges.
- Molybdenum (Mo):
Molybdenum offers a balance between a high melting point (2623°C) and better machinability compared to tungsten. Its thermal and mechanical properties make it suitable for use in rocket nozzles, especially when coated with protective layers to enhance its oxidation resistance.
- Tantalum (Ta):
Tantalum is another refractory metal with a high melting point (3017°C) and good corrosion resistance. Its ability to form stable oxides at high temperatures makes it suitable for nozzle applications in corrosive environments. However, like tungsten, tantalum is dense and can be challenging to machine.
2. Ceramic Materials
- Silicon Carbide (SiC):
Silicon carbide is widely used in rocket nozzles due to its excellent thermal stability, high hardness, and resistance to thermal shock. It can withstand temperatures up to 2700°C, making it suitable for high-performance propulsion systems. SiC’s low density compared to refractory metals also reduces the overall weight of the nozzle, which is advantageous in aerospace applications.
- Zirconium Dioxide (ZrO2):
Zirconium dioxide, or zirconia, is valued for its high melting point (2715°C) and low thermal conductivity, which helps in maintaining the structural integrity of the nozzle at high temperatures. Zirconia-based composites are often used in thermal barrier coatings to protect the underlying materials from extreme heat.
- Gadolinium Zirconate (Gd2Zr2O7):
Gadolinium zirconate is known for its exceptional thermal and chemical stability, resistance to thermal shock, oxidation, and corrosion, and low thermal conductivity. These properties make it suitable for high-temperature applications such as thermal barrier coatings in aerospace and gas turbine engines.
3. Composite Materials
- Carbon-Carbon Composites:
Carbon-carbon composites are a mainstay in rocket nozzle design due to their high thermal resistance and lightweight properties. These composites consist of carbon fibers embedded in a carbon matrix, offering exceptional strength-to-weight ratios and the ability to withstand temperatures exceeding 3000°C. Their low thermal expansion further enhances their suitability for high-temperature applications.
CMCs, such as silicon carbide fiber-reinforced silicon carbide (SiC/SiC), combine the advantages of ceramics and composites. They provide high thermal resistance, low density, and improved toughness compared to monolithic ceramics. CMCs are increasingly being used in rocket nozzles due to their ability to withstand extreme thermal and mechanical stresses.
4. Superalloys
- Inconel:
Inconel is a family of nickel-chromium-based superalloys known for their high strength and resistance to oxidation and corrosion at elevated temperatures. Inconel alloys, such as Inconel 718, are often used in rocket nozzles where a balance between strength, toughness, and corrosion resistance is required. These superalloys can maintain their mechanical properties at temperatures up to 700-800°C.
- Haynes 188:
Haynes 188 is a cobalt-based superalloy that offers excellent high-temperature strength and oxidation resistance. It is commonly used in rocket nozzles and other hot gas path components due to its ability to withstand temperatures up to 1100°C without significant degradation.
Conclusion
Selecting the right material for rocket nozzles is crucial for the efficiency and reliability of propulsion systems. Refractory metals, ceramics, composites, and superalloys each offer unique properties that address the extreme conditions experienced by rocket nozzles. Advances in material science continue to drive the development of new and improved materials, ensuring that future rocket engines can operate more efficiently and withstand even harsher environments. For more information, please check Advanced Refractory Metals (ARM).
Related Posts
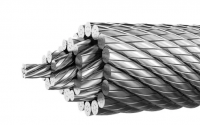
Tungsten Wire Rope for Diverse Applications
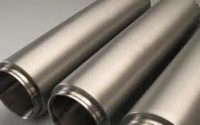
Various Application Fields of Molybdenum Coating
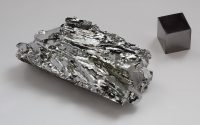