Methods to Improve the Recovery Rate of Molybdenum
Properties of Molybdenum
Molybdenum is a silver-white refractory metal with a melting point of 2615°C and a density of 10.2 g/cm3. Its coefficient of expansion is small, almost the same as that of the special glass for electron tubes, about 4.8 µm·m−1·K−1 (25 °C). Molybdenum is very stable at room temperature. When it is higher than 600℃, it will react with air and be rapidly oxidized to molybdenum oxide. Molybdenum can resist the corrosion of dilute sulfuric acid, hydrofluoric acid, phosphoric acid, etc., but it is not resistant to the corrosion of nitric acid, aqua regia, and molten salt with strong oxidizing properties. Molybdenum does not react with hydrogen, but molybdenum powder can absorb hydrogen. Molybdenum reacts with carbon, hydrocarbons, or carbon monoxide above 800°C to form molybdenum carbide. Molybdenite is the main molybdenum mineral with industrial value. Other secondary minerals of molybdenum include molybdenum-tungsten calcium ore, iron-molybdenum ore, lead-molybdenum ore, and molybdenum-copper ore.
Uses of Molybdenum
Molybdenum is widely used in the metallurgical industry as a well-regarded alloying additive. Adding an appropriate amount of molybdenum to steel and iron can improve their strength, toughness and corrosion resistance. The amount of molybdenum added in the production of nickel-based alloys is more than that of other alloys, about 15%-30%. Molybdenum can greatly improve the corrosion resistance of nickel-based alloys. Nickel-based alloys containing 18% molybdenum and 18% chromium can withstand high temperatures of 1093°C. A molybdenum-rhenium alloy containing 50% molybdenum and 50% rhenium has good high-temperature properties, and this alloy tube can be used close to the melting point.
Molybdenum is widely used in the electronics industry, such as silicon wafer supports, new light source electrode lead wires, etc.
Molybdenum can be used as high-temperature resistant components in the aviation and aerospace industries.
Molybdenum compounds can be used as catalysts and reagents, and can also be used to formulate pigments.
Molybdenum disulfide solid lubricant is known as the “King of Lubrication”.
Molybdenum is also one of the best trace element fertilizers in agriculture.
Read more: Molybdenum Facts and Uses
Recovery of Molybdenum
Molybdenum is a precious and rare metal. In the production of ferromolybdenum, the cost of molybdenum ore accounts for 97.5% of the total cost. Therefore, it is very important to maximize the recovery rate of molybdenum to reduce costs and improve economic benefits. The recovery rate of molybdenum can be improved from two aspects: on the one hand, strictly control the links that may cause molybdenum loss to reduce unnecessary loss of molybdenum; on the other hand, recover as much molybdenum from waste as possible.
1) MoO3(s) has high vapor pressure and is easy to sublime. Therefore, reducing the sublimation amount of MoO3(s) and recovering molybdenum-containing dust are important links that must be paid attention to.
2) In the roasting of molybdenum concentrate, the roasting temperature should be accurately controlled, the sublimation of MoO3(s) should be minimized, and an efficient purification system should be required to re-roast the recovered molybdenum dust.
3) Use a furnace body with a high degree of sealing. In smelting, the sealed furnace body can not only reduce heat loss, and reduce the amount of aluminum reducing agent, but also reduce the loss of molybdenum in the slag, and is also conducive to the purification and dust removal of flue gas. The molybdenum-containing dust collected by the dust collector can be returned to smelting after being agglomerated. If the dust contains other metal elements, the comprehensive utilization of the dust should be considered.
4) The ferromolybdenum particles mixed in the ferromolybdenum slag must be recovered, and the slag can be crushed and recovered by magnetic separation.
5) Finishing chips and furnace bottom nodule iron are the largest amount of molybdenum-containing return materials and should be added to cooked molybdenum ore for re-smelting.
For more information, please visit https://www.samaterials.com/.
Related Posts
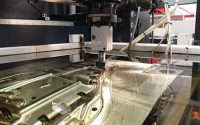
Technical Guide to Molybdenum Wire Cutting Processes
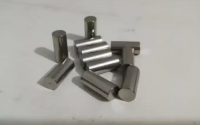
Understanding the Distinction Between TZM and TZC Alloys
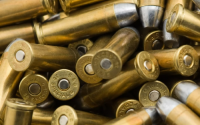