Understanding the Distinction Between TZM and TZC Alloys
Introduction
In the realm of high-performance alloys, TZM and TZC stand as prominent members. Each of them offers unique compositions and properties, and they cater to distinct industrial demands. While both are rooted in molybdenum (Mo), their nuanced compositions and resulting properties set them apart. So, they become vital in diverse applications across industries reliant on high-temperature stability, strength, and wear resistance.
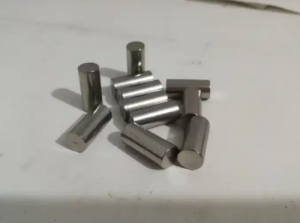
TZM and TZC Alloys
Let’s have a detailed discussion about their differences and similarities.
TZM Alloy: Composed for High-Temperature Prowess
TZM is an acronym derived from its primary constituents—titanium (Ti), zirconium (Zr), and molybdenum (Mo). It is renowned for its exceptional high-temperature strength and stability. This alloy typically comprises around 0.5% titanium, 0.08-0.4% zirconium, with molybdenum forming the rest. Its hallmark properties include remarkable resistance to thermal creep, superior stability at elevated temperatures, and notably low thermal expansion. These properties contribute to dimensional stability even in extreme conditions.
Applications of TZM:
TZM finds widespread application in industries such as aerospace, defense, nuclear reactors, and high-temperature furnaces. In aerospace, it plays a pivotal role in critical components requiring structural integrity and stability at soaring temperatures. Its presence in nuclear reactors extends to applications demanding high-temperature strength. Its use in high-temperature furnaces ensures durability and reliability in extreme thermal environments. The semiconductor industry also benefits from TZM because it has the ability to withstand high-temperature processing conditions.
Related reading: TZM Alloy Vs Pure Molybdenum
TZC Alloy: Embracing Enhanced Hardness and Wear Resistance
TZC, in contrast, represents a composite alloy incorporating molybdenum as its base. It is complemented by titanium carbide (TiC) and zirconium carbide (ZrC) particles distributed within the molybdenum matrix. This composite nature elevates its properties and endows it with increased hardness, wear resistance, and potential enhancements in strength compared to TZM.
Applications of TZC:
TZC’s fortified hardness and wear resistance find application in tooling, dies, cutting tools, and various industrial applications because abrasion and wear are predominant concerns. With these enhanced properties, it has become a preferred choice in various applications. Thanks to increased hardness and improved wear resistance, it is critical for prolonged tool life and performance efficiency.
Distinguishing Characteristics
The fundamental contrast lies in their composition and resulting properties (See Table 1). While TZM prioritizes high-temperature stability and strength, TZC capitalizes on reinforced hardness and wear resistance derived from the presence of carbide particles within the molybdenum matrix.
Both alloys play pivotal roles across industries, albeit in different niches. TZM thrives in environments requiring structural integrity and stability at extreme temperatures, while TZC shines in applications demanding enhanced hardness and wear resistance.
Distinction between TZM and TZC Alloys
Property | TZM | TZC |
Composition | Molybdenum (Mo), Titanium (Ti), Zirconium (Zr) | Molybdenum (Mo), Titanium (Ti), Zirconium (Zr), Carbon (C) |
Carbon Content | Does not contain carbon | Contains carbon |
Strength | High | Very high |
Ductility | Lower than TZC | Higher than TZM |
Temperature Resistance | Excellent | Superior |
Application | Aerospace, defense, and high-temperature applications | High-stress and high-temperature applications, particularly in the aerospace industry |
Weldability | Good | Fair |
Conclusion
In essence, TZM and TZC epitomize the ingenuity of materials science, catering to a spectrum of industrial demands by leveraging distinct compositions and finely tuned properties to confront the rigors of diverse operational environments. Their unique contributions underscore their significance in advancing technology and sustaining critical operations across multiple industries.
Advanced Refractory Metals (ARM) is a reliable source for pure molybdenum and its alloys. ARM has various forms and dimensions and provides flexibility for different industrial needs. Both TZM and TZC are available. If you’re looking for specific information or have any questions, feel free to contact us at https://www.refractorymetal.org/.