Molybdenum Wire Cutting in Aerospace and Beyond
Introduction
In the ever-evolving landscape of aerospace engineering and advanced manufacturing, the quest for precision and innovation has led to the adoption of cutting-edge technologies. Among these, molybdenum wire cutting stands out as a powerful and versatile method. It plays a crucial role in shaping the future of aerospace components and beyond.
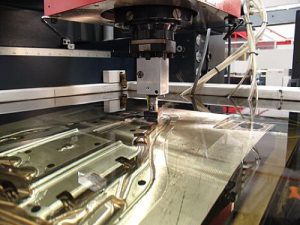
This article is going to explore these uses in the aerospace industry and beyond. Hope that you can have a better understanding of their properties and applications.
The Marvel of Molybdenum:
Molybdenum is a refractory metal renowned for its high melting point and exceptional mechanical properties.
- With a melting point exceeding 2,600 degrees Celsius, Mo demonstrates superior heat resistance. It has become an invaluable component in high-temperature applications such as aerospace and industrial furnaces.
- Its robust mechanical characteristics include impressive tensile strength and resistance to corrosion. So, Mo is crucial in the production of durable and reliable materials for various engineering and manufacturing purposes.
Mo takes center stage in wire-cutting applications. With a melting point of approximately 2623 degrees Celsius, this metal possesses the thermal stability required for processes involving extreme temperatures. This makes it an ideal candidate for aerospace components subjected to intense operating conditions.
Related reading: Why Can Molybdenum Wire Cut Metal?
The EDM Revolution:
Electrical Discharge Machining (EDM) is a non-traditional machining process. It has witnessed a revolution with the integration of molybdenum wire as the cutting tool. This method involves the controlled generation of electrical discharges between the molybdenum wire and the workpiece. This method results in precise material removal.
1. Precision Engineering:
Aerospace applications demand unparalleled precision, and molybdenum wire cutting delivers exactly that.
The thinness of the wire often ranges from micrometers to millimeters. It allows for the creation of intricate shapes and fine details with micron-level accuracy. This capability is crucial for producing components like turbine blades, nozzles, and intricate structural elements in aircraft and spacecraft.
2. Thermal Stability in the Crucible of Aerospace:
One of the distinctive features of molybdenum wire cutting is its ability to withstand extreme temperatures.
Aerospace components, especially those in propulsion systems, experience intense thermal conditions during operation. Molybdenum’s high melting point ensures the structural integrity of the wire. Also, the high melting point allows it to endure the rigors of the EDM process without compromise.
Applications across the Aerospace Spectrum:
–Turbine Components:
In the aerospace industry, turbine components operate in an environment of extreme temperatures and mechanical stress. Molybdenum wire cutting is instrumental in shaping turbine blades and vanes with intricate cooling channels. In this way, Mo optimizes performance and efficiency.
–Rocket Nozzles:
For space exploration and satellite launches, precision in propulsion systems is paramount. Molybdenum wire cutting contributes to the manufacturing of rocket nozzles. That’s because its thermal stability and precision play a vital role in directing and accelerating exhaust gases.
–Structural Elements:
Aerospace structures demand lightweight yet robust components. Molybdenum wire cutting enables the creation of intricate structural elements that contribute to the overall strength and durability of airframes and spacecraft.
–Beyond Aerospace: Expanding Horizons:
While molybdenum wire cutting has found a natural home in aerospace, its applications extend far beyond the bounds of the atmosphere. The method is embraced in various industries, including medical devices, electronics, and toolmaking. In these fields above, precision and reliability are non-negotiable.
The Future of Manufacturing:
As technological advancements continue to reshape the manufacturing landscape, molybdenum wire cutting stands at the forefront of innovation. Its ability to produce complex geometries comes with its adaptability to various materials. Thus, it has become a key player in the future of high-precision manufacturing.
Conclusion
Molybdenum wire cutting comes with exceptional properties and applications. It has become a cornerstone in the pursuit of precision engineering, particularly in the aerospace sector.
As the aerospace industry reaches new heights and manufacturing technologies evolve, molybdenum wire cutting remains a symbol of the relentless commitment to pushing the boundaries of precision machining.
From turbine blades to rocket components, its impact is felt across the skies and beyond. All these attributes mark a new era in the world of advanced manufacturing. For more information, please check samaterials.com.
Reference:
[1] https://en.wikipedia.org/wiki/Electrical_discharge_machining