Preparation and Application of Molybdenum Products
Molybdenum and molybdenum alloy products, such as molybdenum plate, molybdenum rod, molybdenum wire, molybdenum tube, molybdenum foil, etc., are prepared by powder metallurgy and subsequent deformation processing technology.
The mixed molybdenum and molybdenum alloy powders are first made into green compacts by conventional pressing or isostatic pressing techniques. The compacts are then sintered in a protective atmosphere of hydrogen at a high temperature of 2000-2200°C to increase their strength and density and make them suitable for further deformation processing. The sintered billets are extruded, forged, rolled, or swaging in the temperature range of 1200-1500°C. The density of the material increases as the number of deformations increases.
Forgings, round bars, and sheets are produced by the above process. Thick wire is prepared by high-temperature rolling and drawing, and the filament is prepared by low-temperature drawing.
Pure molybdenum has a melting point of up to 2620°C. High melting point and high-temperature strength enable the material to be used at high temperatures of 1900°C; depending on the area shrinkage during processing, molybdenum can recrystallize between 800°C and 1200°C; 1600°C to 1800°C, the spontaneous grains become larger, resulting in a significant decrease in strength and hardness.
Due to its good high-temperature mechanical stability, molybdenum and molybdenum alloys, molybdenum machining parts have many applications.
- Lighting industry: supporting tungsten molybdenum rods, molybdenum pins, molybdenum hooks, and molybdenum rings in traditional incandescent lamps; tungsten stranded core rods; low and high-pressure mercury lamps and halogen lamps for sealing with quartz glass molybdenum tape; Shields for reducing the brightness of automotive headlights; high-temperature molybdenum wire for automotive and motorcycle headlight struts.
- Electronic tube industry: molybdenum wire is used for vacuum-tight connection with borosilicate glass in electronic tubes, especially molybdenum pins with the polished surface; a grille made of molybdenum wire that can withstand huge thermal stress; used to improve electronic Gold-plated molybdenum wires with emission characteristics; anodes, auxiliary anodes, cathode support elements and other structural parts in electron tubes such as launch tubes, short-wave tetrodes, and high-power tetrodes; molybdenum end caps and molybdenum pins in microwave magnetrons, and etc.
- Semiconductor technology: Molybdenum has been widely used in transistors and semiconductor components.
- Switches and contacts: mercury switches and special contacts for telephone relays.
- Isothermal forging: Molybdenum or TZM isothermal forging dies for titanium alloys and superalloys with high mechanical stability in the temperature range of 900-1100°C.
- Nuclear technology: sintering units, sintering boats, and sintering discs for nuclear fuel manufacturing, high-temperature flow elements for exterior wall protection, and reversing modules in nuclear fission units.
- Lighting industry: arc starting electrodes for discharge tubes, filaments, filament annealed tungsten tubes, evaporation boats, welding electrodes, etc.
- Electronics industry: semiconductor substrates, electron tube grids, anodes, passive cooling device radiators, capacitor sintering boats, and cups, etc.
- Medical systems: X-ray targets and their fasteners, fixed anodes, detector components, collimators, shields, containers, and accessories。
- High-temperature furnace manufacturing: heating element, heat shield, material rack, and other components, sintering boat, fasteners, etc.
For more information, please visit https://www.samaterials.com/.
Related Posts
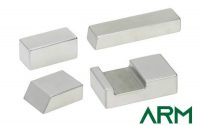
How to Select Bucking Bar Materials
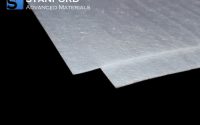
Silica Aerogel Felt: A Leap Forward in Thermal Insulation
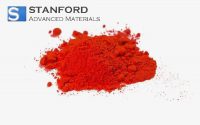