Factors Affecting the Lifespan of Molybdenum Electrodes in the Glass Industry
Introduction
Molybdenum electrodes play a crucial role in the glass manufacturing process. They are used to create uniform electric fields that melt and shape the glass, and therefore, their lifespan is critical for the success of the production line. However, the lifespan of molybdenum electrodes can be affected by various factors.
Glass composition
The chemical composition of the glass can have a significant impact on the lifespan of molybdenum electrodes. Some glass compositions, such as high levels of alkalis or halides, can be corrosive to molybdenum, leading to faster electrode degradation. In addition, glasses with high levels of certain impurities, such as iron or copper, can also cause accelerated electrode degradation.
Operating temperature
The operating temperature can also have a significant impact on the lifespan of molybdenum electrodes, such as accelerating the oxidation and corrosion of the electrodes, thereby reducing their lifespan. That’s because, at high temperatures, molybdenum reacts with oxygen and other elements in the glass melt, causing the formation of oxides and other compounds that weaken the electrodes and make them more susceptible to corrosion. Additionally, higher temperatures also increase the rate at which impurities diffuse into the electrodes, which further accelerates their degradation.
Electrical current
The service life of molybdenum electrodes in the glass industry can also be affected by the amount of electrical current that passes through them. Higher currents cause the electrodes to degrade faster due to the increased heat generated and the formation of hot spots. This causes localized melting and deformation of the electrodes, weakening them and making them more susceptible to corrosion and other forms of degradation. What’s worse, higher currents also increase the rate at which impurities diffuse into the electrodes, which further accelerates their degradation.
Electrode design
The design of molybdenum electrodes also matters. Factors such as electrode size, shape, and surface area all affect their durability and corrosion resistance. For example, electrodes with larger surface areas may be more susceptible to oxidation and corrosion due to greater exposure to the glass melt. Likewise, electrodes with complex shapes or sharp corners may be more susceptible to stress and deformation, which can weaken them and make them more prone to failure.
Maintenance and cleaning
The lifespan of molybdenum electrodes in the glass industry can be significantly increased through proper maintenance and cleaning. By regularly cleaning and inspecting them, any issues that may lead to premature failure can be identified and addressed early on. For instance, removing any accumulated deposits or impurities from their surface can prevent corrosion and other forms of degradation. In addition, frequent inspections can reveal any signs of wear or damage, such as cracks or bending, which can be repaired or replaced before they escalate into more serious problems. Proper handling and storage of these electrodes is also important in preventing damage and ensuring their good condition during downtime.
Conclusion
In conclusion, the lifespan of molybdenum electrodes in the glass industry is influenced by several factors. Glass composition, operating temperature, electrical current, and electrode design all play a role in determining how long the electrodes will last. Additionally, proper maintenance and cleaning practices are crucial in extending their service life and ensuring reliable performance. By paying attention to these factors, glass manufacturers can maximize the lifespan of their molybdenum electrodes and minimize downtime, thus achieving efficient and cost-effective production processes.
For more information about molybdenum materials, please visit https://www.samaterials.com/6-molybdenum.html.
Related Posts
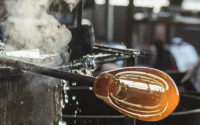
Molybdenum Electrodes vs. Traditional Glass Melting
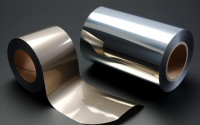
Molybdenum Foil vs. Tungsten Foil: A Comparative Analysis
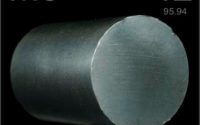